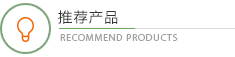
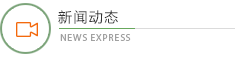

工業(yè)內(nèi)窺鏡搭載三維立體相位掃描測(cè)量技術(shù)在發(fā)動(dòng)機(jī)孔探中的應(yīng)用
一、從韋林工業(yè)內(nèi)窺鏡看工業(yè)視頻內(nèi)窺鏡測(cè)量技術(shù)的發(fā)展歷程
工業(yè)內(nèi)窺鏡的誕生是為了實(shí)現(xiàn)間接目視檢查,而它應(yīng)用于民航發(fā)動(dòng)機(jī)孔探工作時(shí),操作者除了需要通過它查找缺陷,還需要對(duì)缺陷尺寸進(jìn)行測(cè)量,以便滿足視情維護(hù)的要求。為了得到有判定價(jià)值的數(shù)據(jù),最初采用接觸式測(cè)量法,即在光學(xué)硬桿鏡或柔性光纖鏡探頭上捆綁已知尺寸的參照物,通過它與被測(cè)物的直接接觸人為地比較估算缺陷實(shí)際尺寸的大小。這種方法增加了探頭的外徑,并嚴(yán)重影響了探頭的導(dǎo)向性能, 導(dǎo)致發(fā)動(dòng)機(jī)內(nèi)部需要檢測(cè)的很多區(qū)域無(wú)法到達(dá),且可能造成參照物因卡阻而脫落,形成發(fā)動(dòng)機(jī)內(nèi)部的多余物隱患。
隨著美國(guó)韋林工業(yè)內(nèi)窺鏡在1984 年研制出全球第一臺(tái)工業(yè)視頻內(nèi)窺鏡產(chǎn)品以后,通過視頻成像處理技術(shù)實(shí)現(xiàn)了非接觸式的比較測(cè)量方法,很好地解決了上述問題。這種比較測(cè)量法是使用發(fā)動(dòng)機(jī)內(nèi)已知機(jī)構(gòu)的尺寸作為參數(shù),通過圖像處理軟件進(jìn)行比較計(jì)算,從而得到測(cè)量數(shù)據(jù)。如將葉片氣孔間距作為已知參考值,對(duì)該葉片上的缺陷尺寸進(jìn)行分析測(cè)量。該方法要求已知尺寸與未知缺陷在同一平面上,且探頭的鏡頭與該平面相對(duì)垂直,才能實(shí)現(xiàn)測(cè)量計(jì)算并具有起碼的相對(duì)準(zhǔn)確度。在遇有較大尺寸的缺陷且測(cè)量精度要求不高時(shí),可以選用該測(cè)量技術(shù)。目前具有測(cè)量功能的工業(yè)視頻內(nèi)窺鏡產(chǎn)品都有該測(cè)量方式。但對(duì)于民航發(fā)動(dòng)機(jī)孔探工作需要檢查的很多位置,操作者很難在相對(duì)垂直的同一平面上找到可作為比較計(jì)算參數(shù)的已知尺寸,并且這種測(cè)量的精確度仍不能完全滿足要求。
美國(guó)韋林工業(yè)內(nèi)窺鏡在上世紀(jì)九十年代初所研發(fā)的單物鏡陰影測(cè)量法技術(shù)首次實(shí)現(xiàn)了孔探工作中的精確測(cè)量,這種測(cè)量法是工業(yè)視頻內(nèi)窺鏡上最早應(yīng)用的非接觸式精確測(cè)量技術(shù)(見圖1),其在視頻探頭的測(cè)量鏡頭的照明光輸出窗口刻有一道黑色直線, 當(dāng)照明光通過時(shí),會(huì)在被測(cè)物體上形成一條陰影線,探頭距離物體的遠(yuǎn)近變化使陰影線在屏幕上的位置左右移動(dòng)變化,而測(cè)量鏡頭上的單一物鏡的成像視角不變,主機(jī)內(nèi)的視頻成像處理器會(huì)根據(jù)直角幾何運(yùn)算原理計(jì)算出測(cè)量鏡頭與被測(cè)平面的距離,從而進(jìn)一步在該平面上計(jì)算獲得測(cè)量點(diǎn)的二維坐標(biāo),以便進(jìn)行各種測(cè)量模式下的精確測(cè)量(見圖2)。這種測(cè)量法的缺點(diǎn)同樣是要求測(cè)量鏡頭與被測(cè)面相對(duì)垂直(不垂直時(shí),只能沿陰影線進(jìn)行測(cè)量)才能保證測(cè)量精度,因而操作難度相對(duì)較高,應(yīng)用上有一定的局限性。
為了解決這一問題,隨后又出現(xiàn)了雙物鏡測(cè)量技術(shù),用測(cè)量鏡頭上的兩個(gè)物鏡(見圖3)之間的已知距離作為底邊,通過與測(cè)量點(diǎn)所形成的頂角大小的變化,建立準(zhǔn)確的三角幾何計(jì)算關(guān)系計(jì)算確定測(cè)量點(diǎn)與鏡頭的距離, 并通過灰度識(shí)別區(qū)分不同的測(cè)量點(diǎn), 進(jìn)而計(jì)算獲得測(cè)量點(diǎn)的坐標(biāo),以便進(jìn)行各種模式下的精確測(cè)量(見圖4)。由于采用夾角變化作為變量,不再需要鏡頭與被測(cè)物體垂直,一定程度上降低了孔探測(cè)量操作的難度和強(qiáng)度。但根據(jù)雙物鏡的設(shè)計(jì)原理,其鏡頭的視野相對(duì)單物鏡減半,屏幕圖像也被一分為二,不便于觀察尋找及定位缺陷,所能測(cè)量的區(qū)域和缺陷大小也相對(duì)明顯受限,并且測(cè)量點(diǎn)的位置及其匹配值(用來(lái)衡量選取的測(cè)量點(diǎn)識(shí)別合格與否的標(biāo)準(zhǔn))正確與否,存在人為及系統(tǒng)誤差的可能性。
無(wú)論是單物鏡陰影測(cè)量法還是雙物鏡測(cè)量法,都是基于二維畫面進(jìn)行處理和計(jì)算的,并且變量參數(shù)(位移或夾角)少、三角幾何計(jì)算的數(shù)學(xué)模型單一。為保證測(cè)量精度就要有較大的放大倍數(shù),為此測(cè)量鏡頭的視野和焦距范圍都偏小。需要首先使用視野范圍相對(duì)較廣、焦距范圍相對(duì)較大的觀察鏡頭尋找并發(fā)現(xiàn)缺陷之后,將探頭取出更換成測(cè)量鏡頭,然后再次穿入發(fā)動(dòng)機(jī)尋找缺陷進(jìn)行測(cè)量。由于這兩類測(cè)量鏡頭的視野很?。?0°或60°)、焦距較近,很難快速有效地再次尋找到并達(dá)到缺陷位置,甚至有可能找不到缺陷;即便到達(dá)缺陷所在的葉片位置,也有可能因?yàn)榻嵌然蛞曇暗膯栴},無(wú)法完整地捕捉到缺陷的圖像。當(dāng)面對(duì)超過測(cè)量范圍(如雙物鏡測(cè)量在保證精度的前提下一次測(cè)量范圍一般最大不超過15mm)的較大缺陷時(shí),為了得到相對(duì)精確的數(shù)據(jù),就必須分段測(cè)量,再將結(jié)果累加,嚴(yán)重影響了孔探測(cè)量效率和精度。近些年各型發(fā)動(dòng)機(jī)的孔探穿繞工作呈逐步增多的趨勢(shì),發(fā)現(xiàn)缺陷后取出探頭再次定位測(cè)量,在很大程度上影響了孔探效率,而且多次穿繞增加了探頭的磨損消耗和發(fā)生卡阻的幾率。這就要求工業(yè)視頻內(nèi)窺鏡產(chǎn)品(孔探設(shè)備)具備缺陷的“即發(fā)現(xiàn)即測(cè)量”功能,同時(shí)盡量增大一次性測(cè)量的范圍以及增加更多的測(cè)量模式,以便應(yīng)對(duì)并滿足越來(lái)越多、越來(lái)越復(fù)雜的孔探測(cè)量工作。
已于2005年隸屬于通用電氣(GE) 集團(tuán)的美國(guó)韋林工業(yè)內(nèi)窺鏡于2010年年底推出的三維立體相位掃描測(cè)量技術(shù)可以很好的解決這一問題。該技術(shù)應(yīng)用在其XLG3型工業(yè)視頻內(nèi)窺鏡產(chǎn)品上,通過視頻探頭前端的三維相位掃描測(cè)量鏡頭上的兩個(gè)可見光LED光柵矩陣(見圖5),將頻閃發(fā)射的多條平行陰影線交叉疊加投影到被測(cè)物體表面上,物體表面幾何形狀的變化會(huì)導(dǎo)致出現(xiàn)畸變的條紋(見圖6),這些畸變條紋就包含了物體表面的三維信息。由視頻內(nèi)窺探頭前端的CCD 攝像頭攝取這些三維信息,主機(jī)內(nèi)的計(jì)算機(jī)處理系統(tǒng)再對(duì)此進(jìn)行掃描和運(yùn)算處理, 然后根據(jù)相應(yīng)的數(shù)學(xué)轉(zhuǎn)換模型和重構(gòu)算法對(duì)物體的輪廓進(jìn)行三維重構(gòu),即獲得了被測(cè)物體表面的三維坐標(biāo)數(shù)據(jù),進(jìn)而就可以進(jìn)行各種測(cè)量模式的具體操作,獲得測(cè)量結(jié)果。
二、將搭載三維立體相位掃描測(cè)量技術(shù)的工業(yè)內(nèi)窺鏡應(yīng)用于發(fā)動(dòng)機(jī)孔探工作中的優(yōu)點(diǎn)
三維立體相位掃描測(cè)量技術(shù)應(yīng)用于發(fā)動(dòng)機(jī)孔探工作有以下3方面優(yōu)點(diǎn)。
1. 即觀察即測(cè)量,孔探工作效率高
由于三維立體相位掃描測(cè)量技術(shù)不再是根據(jù)二維畫面進(jìn)行,而是采用攝取和掃描物體表面三維信息的辦法,所以不再限制測(cè)量鏡頭的視野和焦距,可以采用單物鏡且視野范圍更廣、焦距范圍更大的設(shè)計(jì),實(shí)現(xiàn)即觀察即測(cè)量,發(fā)現(xiàn)缺陷后無(wú)需更換鏡頭即可直接測(cè)量(如圖7所示)。近年來(lái),雖然也有其他廠家嘗試研發(fā)觀察鏡頭與測(cè)量鏡頭二合一的技術(shù)以期實(shí)現(xiàn)即觀察即測(cè)量的功能,但由于其測(cè)量精度無(wú)法滿足要求而不被接受。
2. 視野范圍廣、焦距范圍大
該3D鏡頭的視野為105°,屬于廣角鏡頭(見圖8);焦距是8~250mm(前視)、7~250mm(側(cè)視),焦距范圍非常廣,涵蓋了普通觀察鏡頭的極近焦、近焦和中焦的焦距段;適用范圍廣,觀察到的畫面整體更明亮,無(wú)論是檢測(cè)發(fā)動(dòng)機(jī)內(nèi)各級(jí)葉片的狹小空間還是燃燒室等較大空腔(如圖9所示)均能勝任。
3. 測(cè)量結(jié)果更精準(zhǔn)
與單物鏡陰影測(cè)量法和雙物鏡測(cè)量法均是先人為選擇測(cè)量點(diǎn)再進(jìn)行該點(diǎn)的坐標(biāo)計(jì)算不同的是,三維立體相位掃描測(cè)量技術(shù)是通過系統(tǒng)的相位掃描與計(jì)算,首先構(gòu)建出一個(gè)由無(wú)數(shù)的具有三維坐標(biāo)信息的點(diǎn)云集合,然后由操作者選擇測(cè)量模式并選取缺陷測(cè)量點(diǎn),再由系統(tǒng)完成測(cè)量;對(duì)于無(wú)法獲得三維坐標(biāo)也即無(wú)法測(cè)量的區(qū)域直接使用紅色體現(xiàn),系統(tǒng)禁止在這些區(qū)域選取測(cè)量點(diǎn);操作時(shí)不需要陰影線的鑒別、測(cè)量點(diǎn)的匹配等步驟。不僅具有極強(qiáng)的易用性,也意味著盡可能地減少了人為操作誤差,增大了測(cè)量結(jié)果驗(yàn)證的可重復(fù)性,測(cè)量效率高, 測(cè)量結(jié)果更加精確,測(cè)量準(zhǔn)確度可達(dá)97%以上,測(cè)量讀數(shù)在0.01mm位,其中三維點(diǎn)云模型的深度識(shí)別在0.001mm 位,明顯優(yōu)于其他測(cè)量方法,滿足孔探工作中越來(lái)越高的測(cè)量精確要求。
三、多種測(cè)量模式下的比較分析
每一種測(cè)量方法都有很多測(cè)量模式,如長(zhǎng)度、點(diǎn)到線、面積等等,這些模式在采用工業(yè)內(nèi)窺鏡進(jìn)行民航發(fā)動(dòng)機(jī)孔探工作當(dāng)中都有著非常重要的應(yīng)用。
對(duì)于長(zhǎng)度(點(diǎn)到點(diǎn))、折線長(zhǎng)度(多線段)、面積的測(cè)量,單物鏡陰影測(cè)量法、雙物鏡測(cè)量法和三維相位掃描測(cè)量法均可實(shí)現(xiàn),但由于3D鏡頭的單視窗、廣角設(shè)計(jì),一次性有效測(cè)量區(qū)域是其他測(cè)量技術(shù)的兩倍以上。對(duì)于發(fā)動(dòng)機(jī)內(nèi)較長(zhǎng)的裂紋、劃傷或者大面積的涂層脫落以及要確定損傷部位的相對(duì)位置等需要測(cè)量的缺陷或定位,采用三維相位掃描測(cè)量法有可能僅通過一次性操作即可獲得精確的測(cè)量結(jié)果。而采用雙物鏡進(jìn)行分段測(cè)量時(shí),特征點(diǎn)不易被找到,或者邊界點(diǎn)不好確定,有時(shí)為了分區(qū)還需要不斷通過導(dǎo)向操作來(lái)改變鏡頭角度。需要幾次測(cè)量操作之后再將結(jié)果累加,不僅工作量增加而且很難保證測(cè)量精度。較大面積的涂層脫落情況(如圖10所示)使用三維相位掃描測(cè)量法均能夠通過一次測(cè)量得到準(zhǔn)確、有效的缺陷數(shù)據(jù)。
圖7 對(duì)于點(diǎn)到線、深度(點(diǎn)到面) 的測(cè)量,單物鏡陰影測(cè)量法和雙物鏡測(cè)量法雖然也可以實(shí)現(xiàn),但前者需要探頭上的測(cè)量鏡頭與被測(cè)物垂直而不便于操作,后者因?yàn)槠涑上窦皽y(cè)量原理反饋到屏幕上的是二維平面信息,操作者也只能憑借經(jīng)驗(yàn)在二維畫面上人為操作放置測(cè)量點(diǎn),無(wú)法進(jìn)一步驗(yàn)證測(cè)量點(diǎn)在三維空間上選取的位置準(zhǔn)確與否。尤其是對(duì)葉片缺口(見圖11和圖12)和葉尖與機(jī)匣間隙(見圖13和圖14)的測(cè)量,進(jìn)行這種測(cè)量時(shí),很容易把測(cè)量點(diǎn)放在被測(cè)葉片以外的區(qū)域,如另外的葉片上或機(jī)匣上,導(dǎo)致測(cè)量結(jié)果出現(xiàn)嚴(yán)重偏差(見圖15)。而使用三維相位掃描測(cè)量法時(shí),可生成三維點(diǎn)云圖,通過旋轉(zhuǎn)點(diǎn)云圖像,從不同角度檢查所選測(cè)量點(diǎn)的位置準(zhǔn)確性,一旦發(fā)現(xiàn)測(cè)量點(diǎn)位置漂移, 可及時(shí)糾正。真正實(shí)現(xiàn)了測(cè)量后操作者仍可自行檢查測(cè)量點(diǎn)定位是否正確,極大地降低測(cè)量時(shí)出現(xiàn)人為操作誤差的概率。
此外,三維立體相位掃描測(cè)量技術(shù)還增加了深度剖面測(cè)量等新型的測(cè)量模式。僅需選擇兩個(gè)測(cè)量點(diǎn),系統(tǒng)就會(huì)自動(dòng)在兩點(diǎn)之間畫一條線,建立垂直于掃描表面的截面,可以直接得到剖面最深點(diǎn)(見圖16),生成剖面視圖(見圖17),沿剖面的所有點(diǎn)的深度都可以直接測(cè)出,通過三維點(diǎn)云圖(見圖18)可以一次得到測(cè)量區(qū)域內(nèi)最深點(diǎn)的位置和深度值,有助于對(duì)缺陷的形成原因、性質(zhì)及缺陷發(fā)展趨勢(shì)進(jìn)行判斷,有助于對(duì)葉片上的凹坑、掉塊、燒蝕等損傷的深度測(cè)量。若使用雙物鏡測(cè)量法的深度模式,則需要先放置3個(gè)測(cè)量點(diǎn),建立一個(gè)基準(zhǔn)平面,然后在凹坑或掉塊內(nèi)手動(dòng)選取“最深點(diǎn)”,通過深度值的實(shí)時(shí)顯示人為地判斷該區(qū)域最深點(diǎn)位置。因手動(dòng)選點(diǎn)的數(shù)量有限,將導(dǎo)致測(cè)量結(jié)果的可重復(fù)性差,測(cè)量精度不能被保證,且測(cè)量效率低。
四、結(jié)束語(yǔ)
從孔探工作的工作效率、觀察效果、測(cè)量精度以及設(shè)備安全等諸多因素考慮,三維相位掃描測(cè)量技術(shù)是非常適用于發(fā)動(dòng)機(jī)孔探工作的一項(xiàng)先進(jìn)技術(shù)。一套完善的孔探設(shè)備應(yīng)當(dāng)支持三維掃描測(cè)量功能,并兼?zhèn)淦渌愋停ㄈ珉p物鏡測(cè)量、陰影測(cè)量、比較測(cè)量等)的測(cè)量功能,以滿足各種孔探環(huán)境下的測(cè)量需要。
自2010年年底美國(guó)韋林工業(yè)內(nèi)窺鏡推出三維相位掃描測(cè)量技術(shù)以來(lái),該技術(shù)經(jīng)過了發(fā)動(dòng)機(jī)廠家以及國(guó)內(nèi)外眾多航空公司的應(yīng)用驗(yàn)證,其技術(shù)成熟度和實(shí)用性都較高,現(xiàn)已成為了民航發(fā)動(dòng)機(jī)孔探領(lǐng)域的主要測(cè)量技術(shù)。國(guó)航工程技術(shù)分公司成都維修基地于2013年引進(jìn)該項(xiàng)測(cè)量技術(shù),大大提高了孔探工作的效率和精確度。
相關(guān)推薦:相位掃描三維立體測(cè)量工業(yè)內(nèi)窺鏡 MViQ